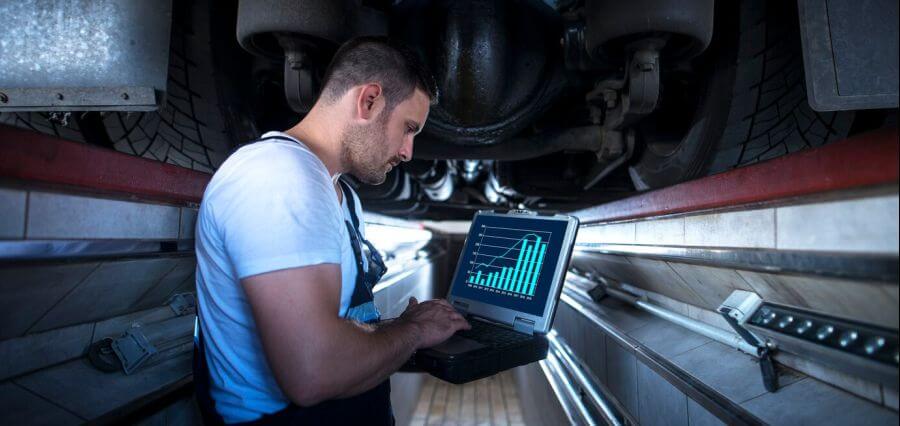
The focus of this article is to improve the process capabilities of wire EDM machines, which aims to improve productivity, reduce costs and achieve automation. Therefore, the requirements for wire EDM machine are much higher than the traditional CNC-controlled equipment.
In the existing wire EDM machine, due to the complexity of different cutting directions, designing a control system for precise workpiece management are needed, in order to improve product quality and output. Combining customized CNC machining technology with the existing arc-cutting methods allows more flexible and efficient machining solutions to achieve higher machining precision and efficiency.
Improving Machine Structure and Component Selection
The development of wire EDM machines primarily relies on the traditional traction method. Its characteristics are:
- First, low machining accuracy, slow cutting speed, and low efficiency;
- Second, low automation levels, the high labor intensity of operators, and high production costs;
- Third, poor product quality, with defects like false threads and false surfaces that are difficult to detect with the naked eye.
Therefore, in future development, outdated semi-automatic CNC wire-cutting machines should be gradually eliminated, and in favor of customized automatic control systems to achieve high-speed operation mode, improve productivity, and reduce workers’ workload.
This requires a newly designed type of wire-cut EDM equipment, namely an improved EDM integrated drive device. It can adjust the feed movement of the cutting area by changing the discharge state of the electrode wire, thereby achieving different effects.
The core component of this mechanism is a variable frequency motor, which increases 5 gears on the original basis to meet different needs, such as precise orientation, feed distance direction, etc.
Improving Electrode Assembly in Wire EDM Machines
To meet the machining requirements of CNC wire-cut EDM machine, the following solutions can be adopted:
First, use a special cable device to fix the wire EDM machine, and then firmly install it on the next electrode through a special clamping force.
Second, the material of the lead screw required for the wire EDM machine is QT, which has relatively low hardness. During machining, it needs to be heat treated to meet the standard requirements, and these steps must be repeatedly adjusted to complete.
Third, due to the characteristics of the EDM and the magnetic conductivity of the electrolyte, a thin film will be formed on the surface of the electrode wire. This film can be relatively thick, making it difficult to ensure the accuracy of the electrode during machining.
Fourth, the magnetic properties of the electrolyte cause a potential difference to form on the surface of the electrode wire. This potential difference corresponds to the voltage of the electrolyte.
The following optimization solutions are proposed to solve the above problems:
First, apply an anti-rust oily solution to the outer wall of the electrode tube to prevent electrode oxidation and improve production efficiency.
Second, apply a polystyrene adhesive sheet to the outer surface of the workpiece, which can also play a certain lubricating role and reduce the wear of the workpiece.
Design and Manufacturing Improvements for EDM Machines
The main function of the wire-cut EDM machine is to convert the wire barrel and screw shaft movement of the electrode wire to the workbench and make it run in a straight line.
The principle of arc discharge is realized by the action of high-voltage power supply, and a certain high temperature and noise will be generated when processing the workpiece. Therefore, in the process of processing the surface of the workpiece, corrosion-resistant materials need to be used to improve its wear resistance. In order to ensure the normal progress of wire-cut EDM processing, a positioning device must be installed on the machine tool guide rail and a protective cover must be placed on the machine tool.
First, when installing on the workbench, the gap must be strictly controlled to prevent instability caused by wear of the contact surface.
Second, when the motor speed is too high, the power supply should be cut off in time to avoid heating and noise caused by excessive current.
Third, when the power of the motor is large, the power supply voltage should be reduced as much as possible to avoid affecting the operating state of the machine. If there are special circumstances, such as high temperature or small grounding resistance, different measures can be used to reduce interference. For example, a three-phase AC power supply can be used in parallel to reduce the incidence of grounding faults; or two DC high-voltage capacitors can be connected in series to achieve the purpose of voltage reduction; the pulse width of the potentiometer can also be adjusted to increase the discharge frequency from the original 1.5Hz to 22kHz.
Improved Machine Debugging and Results
During the process of online cutting EDM, due to the combined influence of various factors, the surface quality is unstable, resulting in a low qualified rate of products, and even serious scrapping. Therefore, when designing it, it is necessary to fully consider various issues and possible hidden dangers of failure, and formulate corresponding solutions.
First, the requirements for the dimensional accuracy of the workpiece. The diameter of the workpiece should be determined according to the position of the aperture of the part hole; the thickness of the workpiece and the roundness of the outer circle should be measured according to the height of the measured aperture.
Second, the selection of performance parameters of the power supply. First, it is necessary to ensure the stability and safety of the power supply voltage, and secondly, to ensure the capacity without load, and to ensure that the reactive power is within the allowable range.
Conclusion
This article mainly focuses on the processing technology principle of wire-cut EDM machine tools, analyzes the existing wire-cut EDM machine tool technology, and provides scientific and feasible structural design solutions for fast-wire EDM wire-cut EDM machines and technical improvement measures for fast-wire EDM wire-cut EDM machines.
With the development and progress of EDM machining, various machines and processes are improving, and the price of EDM wire is also falling. Therefore, to meet market demand, in future development, advanced EDM methods will be chosen to process workpieces, which can not only ensure product quality and precision but also reduce production costs and obtain economic benefits.